Considerations for Selecting a Waterproofing System
- Innovative Waterproofing Solutions
- May 6, 2021
- 4 min read
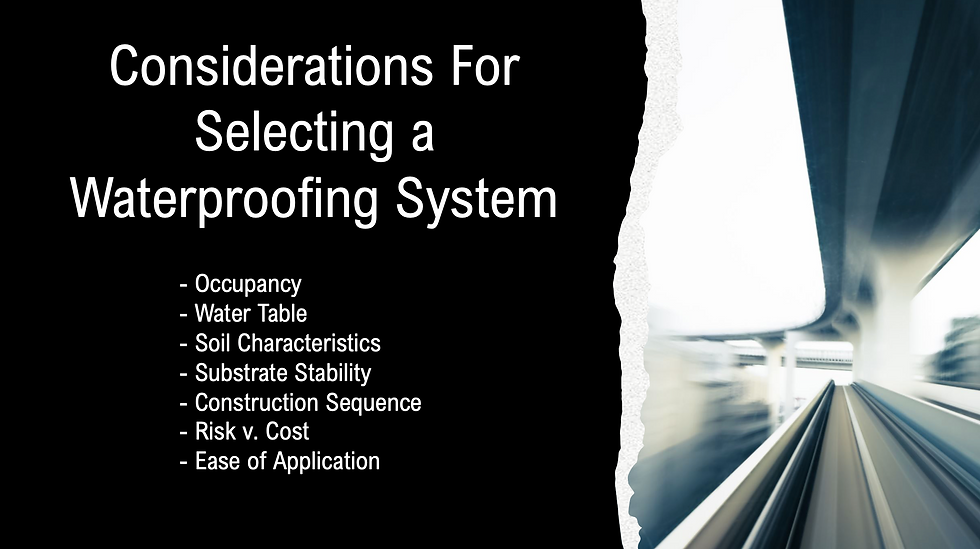
When selecting a waterproofing system conservatism is the watchword. Remember, you only
have the opportunity to do this once! Proper research and due diligence is required to ensure that all waterproofing issues are properly addressed. Site-specific issues and building requirements also necessitate proper consideration.
There are several considerations that an architect or waterproofing designer must examine prior to the selection of a waterproofing system. Some of the considerations are:
- Occupancy
- Water Table
- Soil Characteristics
- Substrate Stability
- Construction Sequence
- Risk v. Cost
- Ease of Application
Occupancy
Important design factors to consider are leak risk tolerance and sensitivity to humidity of an
occupied space. There are certain occupied spaces where leaks can be a detriment. Leaks are intolerable in occupancies with book storage, art storage, computer rooms, electrical switchgear, and medical facilities. These types of facilities also require tight humidity control. Intrusion of air can be as detrimental as water in sensitive facilities. Medical facilities, research and testing laboratories fit within these classifications.
Proper membrane design for the aforementioned facilities would require positive side
waterproofing with a low vapor permeable membrane.
Water Table Level
The water table level is an important consideration that not only determines the type of
waterproofing required, by code it determines if waterproofing is required. The International
Building Code requires that waterproofing or damp proofing is applied on all below-grade
structures where the ground water table is maintained a minimum of 6 inches below the ground slab.
Accurate soil bearings – completed by a competent civil engineer – are required prior to
waterproofing design. In the Northern Hemisphere the water table is usually highest after the spring thaws have saturated the ground and lowest following the summer evaporation of the surface moisture.
Proper waterproofing design should be based on the maximum water table level for the site.
Soil Characteristics
Waterproofing materials are unique because they are exposed to much harsher conditions than any of the other building exterior components. Most of the exposure elements are continuously present at the waterproofing surface and do not dissipate as they do at the other exterior components. For example, water can be present in below-grade surfaces for weeks, whereas water on roof systems is to be removed within 48 hours.
One element to consider is soil characteristics. Chemicals in the soil can have an adverse effect on some materials and knowledge of potential chemicals present is required for design.
Chemical properties in soils can adversely affect waterproofing in various ways. Acids and
alkaline in ground water can accelerate the deterioration of concrete and steel reinforcing bars.
Salt in water corrodes reinforcing bars in concrete. Sulfates can have a negative reaction with
Portland cement resulting in internal shearing stress that causes spalling. Other chemicals that affect waterproofing are calcium hydroxides, oils and chemicals from fertilizer.
The physical properties of the soil can also affect waterproofing. Clay soils of low permeability limit underground hydrostatic pressure. The intensity and nature of hydrostatic pressure can force water into tie-rod holes, cold joints and rock pockets. Hydrostatic pressure can also turn minor imperfections into probable sources of leaks.
Substrate Stability
Waterproofing is applied on substrate surfaces to protect the substrate from structural
deterioration caused by water, chemicals and soil. The applied waterproofing material must also be capable of performance if the substrate becomes unstable or minor imperfections occur.
Some substrates are inherently prone to imperfection and this should be considered prior to
waterproofing design.
Waterproofing membrane applied over substrates that are vulnerable to cracking from any source must be elastic and capable of resealing. Cracks can occur in masonry or other waterproofed components that have multiple construction joints. Damp proofing should not be considered in these conditions.
The types of soils at the site can also have an impact on substrate stability. Expansive soils and peaty soils can produce rising and settling footings that cause cracks in footings and foundation walls. All substrate openings can become potential points of moisture infiltration.
Construction Sequence
Waterproofing is applied in phases as construction of walls and plaza decks are installed. There may be extended periods of time between certain waterproofing applications and final completion. For instance, waterproofing of below-grade walls is typically done in 6- to 8-foot increments from the bottom to the top. The initial section is finished, the site is backfilled, and the waterproofing applicator uses the backfill as a scaffolding to complete the next increment.
This process is continued until the full wall is waterproofed. This process could continue over an extended time period because the waterproofing applicator relies on the pour schedule and backfilling operations.
Installed waterproofing materials are rarely exposed to exterior elements after final application procedures are completed. The membranes are covered by soil, concrete or another type of top surfacing. However, because of the initial construction sequence, these materials may be exposed for an extended period of time. This fact must be considered in the material selection process.
It is important to prevent the exposure of vulnerable materials to the elements when long delays in the schedule occur. Waterproofing materials must be capable of withstanding freezing temperatures if they are to be exposed to these conditions for more than one week. Exposure to rain and water can also be a concern. If bentonite clay is used it must be adequately covered.
Membranes with a low resistance to ultraviolet radiation can deteriorate if the materials are
exposed to sunlight for intervals as short as one month. If the waterproofing is applied prior to the completion of the structural elements it may prompt negative effects on the waterproofing such as deflections or other imperfections.
Risk vs. Cost
The designer should always minimize risk despite any reasonable – or unreasonable – costs. If a building owner or general contractor wants to cut costs, the waterproofing system is not the place to do so. The cost of excavation for repairs – even minor repairs – far exceeds the initial cost of the waterproofing. Remember, as a designer you only have one chance to do it right!
Ease of Application
Ease of application is a minor factor, however, it may result in better workmanship, so it should be considered. There will also be projects where access or space constraints are an issue.
Application methods, particularly material adhesion methods, may be determined by the site constraints. On projects where other factors are in balance, ease of application of a material or a system can be a determining factor in material selection.
The technique of fixing any roof varies, depending on its kind. Flat roofs are easier to repair compared to inclined or pitched roofs. Always hire Roof Repair Oakland Park experts because they have skilled staff, who have the capability to deal with all types of roofs at genuine cost.